硬めの材料の穴あけについて
(HRC30前後)
※本記事は、汎用旋盤での穴あけを前提にしたものとなっています。
普段使用している材料より少し硬い材料に穴をあける時や、
焼き入れをして硬度を上げて使用した物を、再び熱処理して再利用する際に
狙い値よりも少し硬かった時など、
今回はそのような場面にフォーカスして、
「なんだかいつもより材料が硬い気がするんだよなぁ。」
と思われる時の私なりの穴あけの方法を紹介したいと思います。
目次
普段通りに加工すると、ドリルの外刃が摩耗して無くなる
特に軟化処理した材料で、狙い値よりも硬い場合に外刃が溶けてしまう事が多いです。
最初はスムーズにドリルが入って行くのに
加工終盤にキュルキュルと音がしだして切れなくなる場合もあります。
こうなってしまうと、ドリルは研ぎ直しになる上に材料も熱を持って焼きが入って硬くなるのか、
研ぎ直したドリルを使用して再度加工したとしても、
穴のその段差になった部分で再び外刃が欠損してしまうので非常に面倒です。
この場合は反対から穴をあけるか、ボーリングバーなどの切削工具を使用して段差の部分を除去するなどしないといけません。
こうならない為に私は以下の方法で穴あけを行うようにしています。
方法
回転数を落とす
普段よりも回転数を落とします。
硬さにもよるので特に決まった回転数は無く、加工中に少しキツそうだなと思えば
途中でさらに落としたりします。
送りの(ハンドルを回す)スピードを落とす
なるべくゆっくり回し、少しずつ加工していきます。
時間はかかりますが、薄皮を剥いていくような感じで優しく削ります。
注油回数を増やす
普段よりも油をこまめに注すようにしています。
目安は、少しキュルキュル音がしたり、切り粉の色が変色した時などです。
最後に
穴あけの途中でドリルが溶けてしまうのは本当に厄介で、時間も手間も掛かってしまうので
極力避けるべきだと思います。
今回の方法は、私の普段の作業の中での私なりの今の所の最適解です。
なので、他にも色々と方法はあるかも知れません。
これからも経験を重ね、より良い情報を提供できるようにしていきたいと思っています。
少しでも参考になれば幸いです。
当ブログでは、初心者様へ向けたドリルの再研磨方法を紹介した記事もございます。
ご自身で研ぐ事が出来れば、コスト削減にも繋がりますので
興味のある方はぜひご覧ください。
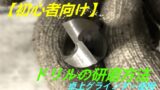
また、YouTube動画もありますのでそちらも是非ご覧ください。YouTubeは更新頻度がかなり遅いですがチャンネル登録していただけると励みになります。
↓その他記事はコチラからどうぞ↓
ご覧頂きありがとうございました。
コメント